
Pulp Flow Meter
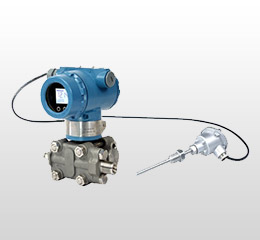
There are many different Teflon resins and processes for manufacturing liners. PTFE is the most common form of Teflon, and generally the best value for most mill flows. When choosing a PTFE liner, select a PTFE liner that is sintered at very high pressures. This manufacturing process randomly meshes the crystalline structure of the Teflon, increasing the liner strength and providing additional chemical resistance. The most common method for forming PTFE liner sleeves is to mold the liner, which results in a directional crystalline structure which is weaker and less resistant to permeation. Rosemount uses a thick sintered PTFE liner on wafer and flanged flow meters
PFA Teflon exhibits similar superior chemical resistance as PTFE Teflon, with improved physical characteristics including higher temperature ratings and higher resistance to permeation. PFA liners should be pure, with no recycled material used as this can result in impurities and voids which can reduce the resistance to permeation. Transfer molding results in a thick, uniform liner which has maximum resistance. A stainless steel retaining mesh welded to the flowtube and retaining grooves are used to secure the liner. PFA liners can extend the useful life in high temperature/aggressive chemical applications, such as hot black liquor in the digesters and the black liquor flow to the recovery boiler.